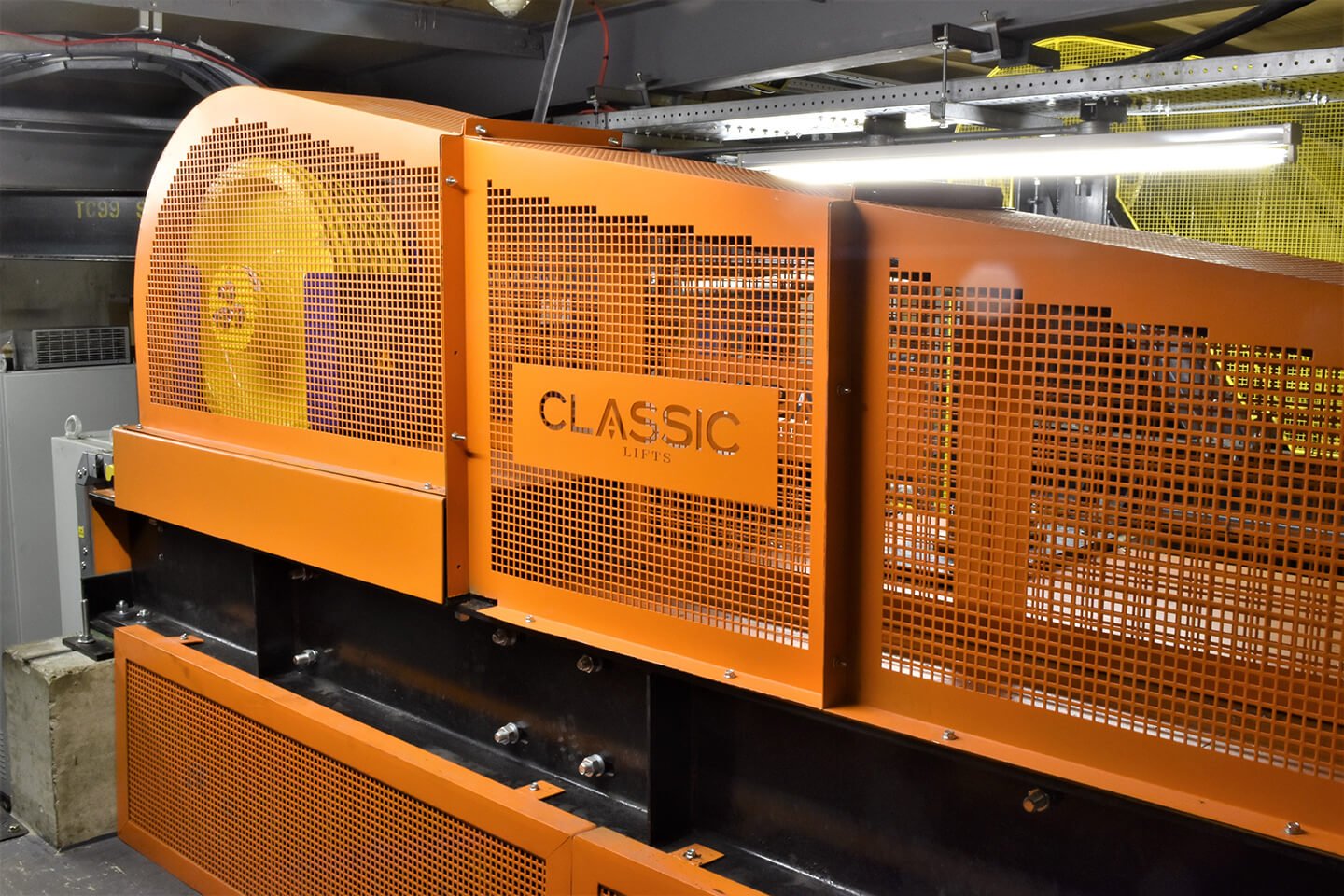
Classic Lifts have worked with The Royal Opera House in Covent Garden, London for 10 years as their maintenance and service provider and were requested to provide a modernisation of two important lifts at the venue.
Working closely with the client, we understood their critical requirements of reducing noise emanating from the lifts and improving the passenger ride quality. In addition, through our experience as service providers, we understood the lifts had fundamental design issues and poor quality components which reduced operational lifetime, caused expensive repairs and affected overall reliability.
Based upon this knowledge and address these challenges, we prepared a fully costed scheme and programme to fundamentally redesign the layout of the lifts within the existing building constraints. Using new technologies, high quality components and alternative materials we were able to simplify the lift configuration and the technological changes of our design achieved significant noise reduction during operation, improved safety, ride comfort and reliability. In addition, our design provided energy savings versus the original installation and the fully modernised lifts being more efficient are less costly to maintain.
The completed installation provides much quieter, smoother operation, much to the delight of our customer.
Classic Lifts were asked to provide costs to complete a partial modernisation of lifts 1 & 2 at The Royal Opera House in Covent Garden, London.
As the incumbent lift contractor and in the absence of architects and consultants we liaised directly with the client to devise a suitable specification and time frame for the works.
There were several challenges to address on this project. We were asked what we could do to reduce noise travelling from the lift installations to the theatre and improve lift ride quality. Also, there were historical problems with ropes and diverters wearing much too quickly meaning costly repairs. These dilemmas could be resolved by thinking a little differently and this started with the existing machine arrangement.
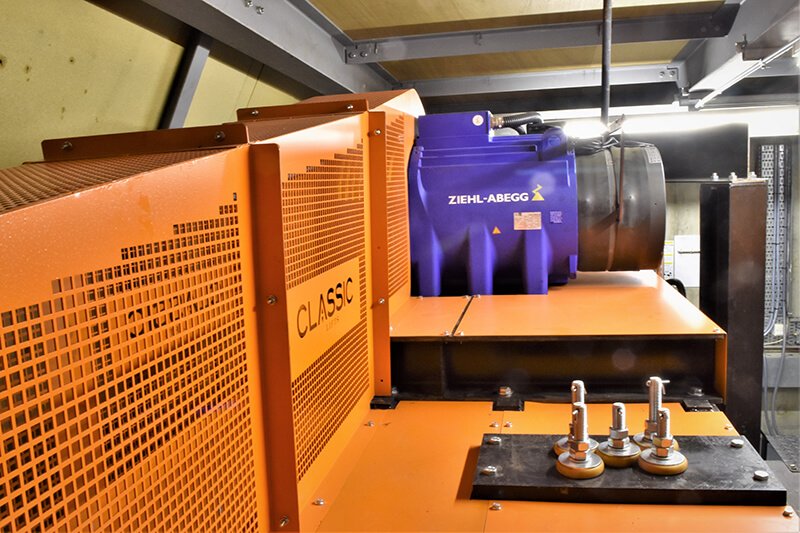
The existing machines were fitted in the motor room above the lift shaft but due to height restrictions they were fitted at low level adjacent to the top of the lift shaft and were side acting. This meant the ropes were vertically twisted via a diverter by 90° over a span of 2M and then diverted across other diverters – four within the motor room and two within the lift shaft. The increased horizontal span of the ropes from the machine diverter to the rear diverter in the motor room caused the ropes to vibrate excessively which contributed to the noise the lift would make whilst travelling. There were also historical problems with two of the diverters frequently failing due to the lateral forces imposed by the side acting arrangement and the ropes needed to be replaced almost every five years due to the amount of twists and turns – what was clear was something had to be done to address this.
Our Technical Director Stephen Turner engaged the support of our supply chain to investigate possible solutions and following consultation and a large amount of preparation we devised a plan to move the new machines to above the lift shaft. This meant we could reduce the number of diverters by two which lessened the horizontal span of the ropes to a much more manageable dimension and remove the diverted vertical 90° twist in the ropes. We also offered further improvements by replacing two of the diverters to heavy duty plastic (Polyamide) which resulted in reduced noise and a much better ride quality. This also offers future savings as the ropes will not need to be replaced as often.
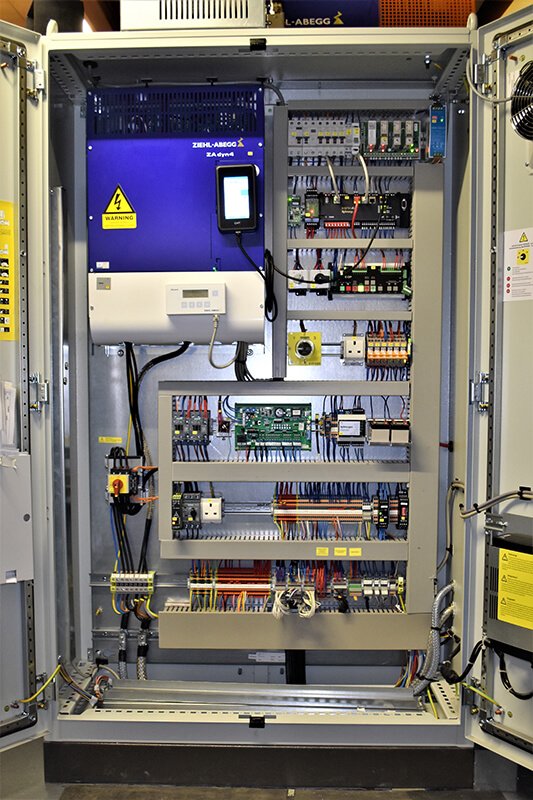
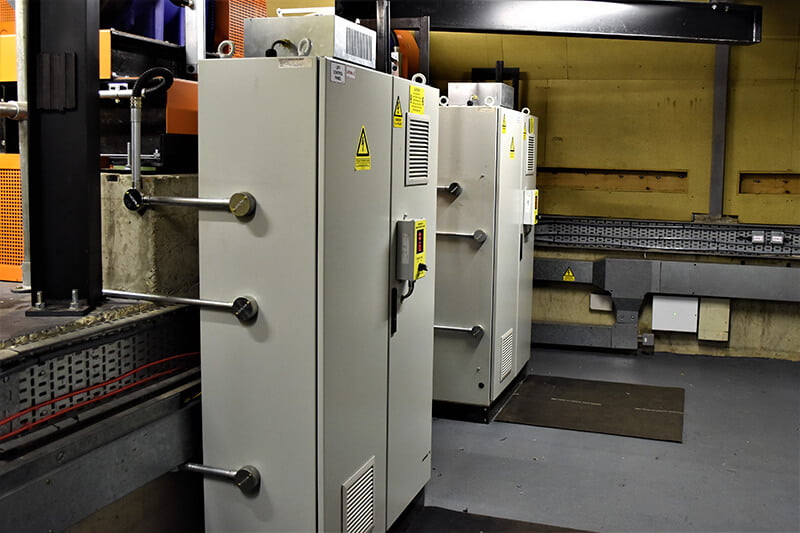
The main motor and gear units were also a source of poor ride quality, so we specified gearless Ziehl Abegg machines. By utilising this technology, we could improve ride quality and reduce noise emanating from the motor room. A by product of using gearless machines is energy saving, it costs a lot less to run these than the traditional arrangement of gears and motors. We were also able to offer Uncontrolled Movement (UCM) and Ascending Overspeed Protection in accordance with EN 81-20.
The final part of the challenge was to reduce noise when the landing and car doors operated. We achieved this by supplying new doors which were soundproofed. Coupled with the superior Kollmorgen control panels and Meiller door drive units we were able to meet the project brief.
The result was vastly reduced noise and a smoother ride quality, much to the delight of the customer.
Contact the team:


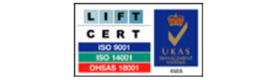
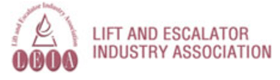
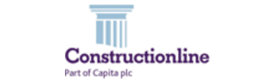
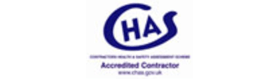
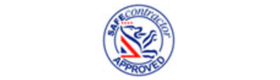
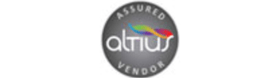
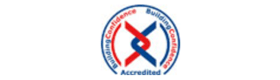
